Installing the machine
In which order do I have to install the components of the S1 & S2?
Checking the scope of delivery
- Unpack the machine and ensure that you have received the following items:
- 1 x Machine S1 / S2, depending on your job
- 1 x Spindle service set
- 1 x Power cable
- 1 x USB cable
- 1 x Compressed air regulator
- 1 x Pneumatic hose
- 1 x Hexagon screwdriver (2.5 mm)
- 1 x Crevice nozzle (for cleaning the working chamber)
- 1 x Key for the emergency release of the working chamber door
- 1 x Calibration set: 1 micrometer, 3 blanks for manufacturing test and calibration specimens, 1 measuring pin
- 2 x Tool magazine inserts
- 1 x Drill bit (2.8 mm) for tool positions
- 1 x Hose connection for the external air extraction unit
Not shown:
- 1 x Brief machine information
- 1 x Transport lock in the working chamber
- 1 x Supplement about removing the transport lock
- 2 x Accessory kit in the working chamber
- 1 x Set of spare screws for the blank holder and the tool magazine cover
-
Packing set
-
1 x Transport box
-
1 x Packaging cushion, multi-part
-
1 x Transport protection cover
-
1 x Housing protection cover
-
- Keep the packaging of the machine, the carrying aid and the transport lock for future transports.

The installation site must meet the following criteria:
- Firm and even surface, must be able to carry the weight of the machine.
- Alternating current source.
- An operational Residual Current Device / Ground Fault Circuit Interrupter on the electric circuit of the machine.
- Machine requires an external air extraction system.
- Machine requires an external compressed air supply.
- Access to the internet.
You can find specific values and additional requirements in the chapter on technical data. Technical data

Damaging of the machine if safety distances are not maintained
If you do not maintain the safety distances, the movable parts of the housing can collide with obstacles when being opened and get damaged. If the ventilation openings are covered, the machine may overheat and get severely damaged.
- Ensure that the following safety intervals are always maintained.

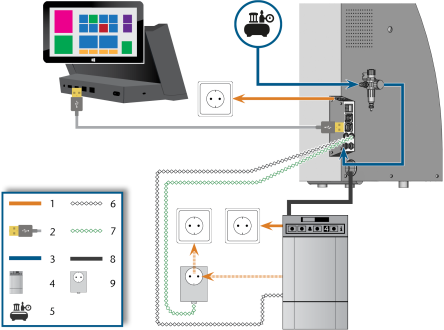
Machine installation (schema)
- Power connection
- USB cable
- Pneumatic hose
- Suction unit
- External compressed air supply
- Data cable of supported suction units (optional)
- Control cable of the switching unit (optional)
- Suction hose
- Switching unit (optional)
You can either use the switching unit including the control cable or the data cable of supported suction units. The data cable must be provided by the manufacturer of the suction unit.
How to install the vhf wet grinding module is described in the operating instructions for the module.
The operating instructions are delivered with the vhf wet grinding module. They are also available for download here.

Damaging of the machine through heavy voltage fluctuations and power surges
Large mains voltage fluctuations and power surges disrupt the control unit and can cause system failures.
- Connect the machine to a separately protected circuit or ensure that no devices are connected that cause severe mains voltage fluctuations when powered on.
- If strong voltage fluctuations cannot be avoided, install a surge protector to safeguard the machine against strong voltage fluctuations.
Short-circuit hazard when the machine is too cold
If the machine is transported from a cold environment into a warmer environment, a short circuit may occur caused by condensate.
- Before switching on the machine after transportation, ensure the following:
- The ambient air has the allowed temperature.
- The machine has the same temperature as the ambient air. This will take at least 48 hours.
- The machine is completely dry.
The machine requires an uninterruptible power supply for proper operation.
- Plug the provided power cable into the power connection at the connection panel of the machine.
-
NOTICE! To avoid job interruptions, install an uninterruptible power supply (UPS), type online / VFI (IEC 62040-3, Class 1) if there are regular power failures or frequent mains voltage fluctuations.
- Insert the plug of the cable into a socket that is protected by a Residual Current Device / Ground Fault Circuit Interrupter.

Before operating the machine for the first time, you must remove the transport lock in the machine working chamber. The transport lock prevents the spindle from getting damaged during transport.
- Ensure the following:
- The machine is connected to the electrical source.
- The CAM computer
The computer that is connected to your machine and which runs dentalcam and dentalcnc. is not connected to the machine.
- Switch on the machine at the main power switch.
- Open the working chamber door.
- Switch off the machine at the main power switch.
- Remove the transport lock as shown in the supplement.

Risk of injuries through leaking compressed air and lashing pneumatic hoses
Open or loose pneumatic connections can cause severe injuries.
- Ensure that during installation and maintenance of the pneumatic hoses and of the compressed air regulator compressed air is not conducted through the hoses and connections.
- Before conducting compressed air through the hoses and connectors, verify that the hoses are securely inserted into the correct connectors and that they are not damaged. This also applies to the compressed air regulator.
- Do not conduct compressed air through damaged hoses and connectors.
Bearing failure and electrical damage to the spindle in case of contaminated compressed air
The incoming compressed air must be dry and oil-free according to ISO 8573-1:2010 because the compressed air regulator only serves as an indicator for contaminated air.
Air purity according to ISO 8573-1:2010 | ||
---|---|---|
Solid particles |
class 3 |
Filtration degree better than 5 µm for solid particles |
Water |
class 4 |
Maximum pressure dew point: +3 °C |
Total oil content |
class 3 |
Maximum oil content: 1 mg/ml3 |
- Ensure that the compressed air meets the above requirements.
- Only connect the machine to the compressed air supply if the compressed air regulator is properly installed.
- Connect the machine to the compressed air supply only via the provided compressed air regulator.
You can find specific values and additional requirements in the chapter on technical data. Technical data
The machine requires the compressed air for the following tasks:
- For the opening and closing of the collet chuck during tool changes.
- For the spindle sealing air which prevents foreign bodies from entering the spindle.
- For the sealing air in the working chamber that keeps machining debris away from sensitive machine parts.

The machine is connected to the external air supply via a compressed air regulator. You can use this regulator to monitor and regulate the pressure of the incoming air.
- 1/8” internal thread, fitted with male compressed air connector to connect the external compressed air supply
- 6 mm push-in fitting to connect the machine.
Failure of the water separator caused by a wrong alignment of the compressed air regulator.
The compressed air regulator must always be mounted in an upright position because otherwise the water separator will not work.
- Mount the compressed air regulator in an upright position.
On the left side of the machine are two bores which you can use to mount the compressed air regulator on the machine.
- Mount the compressed air regulator in an upright position, using the oval-head screws provided in the bores.

The blue compressed air socket must not be confused with the stainless steel socket for cooling liquid. Otherwise the machine will not work properly.
- Close the main external compressed air supply valve.
- Use the provided pneumatic hose to connect the right pneumatic connection of the compressed air regulator to the pneumatic connection of the machine.
- Connect the external compressed air supply to the left pneumatic connection of the compressed air regulator.
- Thoroughly verify that all external pneumatic hoses are properly seated in their corresponding connections and that the hoses and connectors are undamaged.
- If all hoses and connectors are properly installed and undamaged, open the external compressed air supply valve.

Setting the air pressure is only necessary if the air pressure shown by the pressure gauge does not lie between the minimum and maximum air pressure. You can find specific values and additional requirements in the chapter on technical data.
- Rotary knob for pressure regulation
- Pressure gauge for monitoring the outgoing air pressure
- Bowl of the water separator
- Discharge screw
-
Pull the rotary knob on top of the compressed air regulator slightly upwards.
- Turn the rotary knob in the desired direction:
- Turn it in the “+” direction to increase the pressure
- Turn it in the “-” direction to decrease the pressure
- Push the rotary knob down again.
- The knob is locked and cannot be changed inadvertently.

Components of the air extraction system:
Component | Source | Required? | Prerequisite |
---|---|---|---|
Suction unit incl. suction hose |
Customer service, specialist dealers |
Yes |
– |
Switching unit |
Customer service* |
No |
Data cable not used |
Data cable of supported suction units |
Manufacturer of the suction unit |
No |
Supported suction unit; switching unit not used |
Hose connection |
Customer service |
If the suction hose does not fit |
– |
*The switching unit is not available worldwide.

You can find specific values and additional requirements in the chapter on technical data. Technical data
- Use a suction device with the following properties only:
- Designed for the commercial use in the dental sector
- Equipped with a filter of the filter class M
- Equipped with safety devices which protect you from static discharges (e. g. through an anti-static suction hose)

You can install the suction unit as follows:
-
Read the documentation for the suction unit. Follow the operating and safety instructions at any time.
-
Check if the connection of the suction hose has an outer diameter of 45 mm.
-
If the diameter is different, adjust either the hose or the hose adapter supplied with the suction unit.
Alternative: Use the optional hose connection of vhf.
-
Insert the suction hose into the opening for the suction unit on the machine. Make sure that the suction hose is properly seated.
-
Continue with the installation of the suction unit as described in the documentation of the unit.

If you cannot connect the suction hose of the suction unit directly to the machine, install the hose connection as follows:
- Turn the thread of the hose connection counterclockwise until the connection is completely open.
- Insert the suction hose of the suction device completely into the hose connection on the side of the thread.
- Turn the thread of the hose connection clockwise as far as you can.
- Insert the hose connection into the opening for the air extraction system of the machine. Ensure it is firmly connected.
If the thread gets detached from the hose connection, place it onto the connection again and turn it clockwise once so that it is screwed to the connection again.

If you want the machine to automatically switch the suction unit on and off, but a data cable is not available, you can use the optional switching unit. The switching unit is not available worldwide.
- Connect the power cable of the suction unit to the switching unit.
- Connect the control cable of the switching unit to the suction device data port at the connection panel of the machine.
- Plug the switching unit into a power socket.

The transport lock must not be installed when you connect the CAM computer The computer that is connected to your machine and which runs dentalcam and dentalcnc. to the machine. Removing the transport lock
- If you want to control multiple machines with 1 CAM computer
The computer that is connected to your machine and which runs dentalcam and dentalcnc., use our multi-machine control feature. See the documentation for the manufacturing software.
- Switch on the machine at the main power switch.
- Close the working chamber door.
- Start the CAM computer
The computer that is connected to your machine and which runs dentalcam and dentalcnc..
- Use the provided USB cable to connect a USB port of the CAM computer
The computer that is connected to your machine and which runs dentalcam and dentalcnc. to the USB port at the connection panel of the machine.
- Install the newest version of dentalcam & dentalcnc that is released for the machine. If you want to control multiple machines with 1 CAM computer
The computer that is connected to your machine and which runs dentalcam and dentalcnc., use our multi-machine control feature. See the documentation for the manufacturing software.
To determine the USB port number and connect to the machine, select the depicted icon in the Application settings view in dentalcnc.
- dentalcnc will try to establish a connection to the machine. If this is successful, the application will display the port number next to the icon. The machine references.
- If the working chamber door was open during the previous step, close it. If the machine does not reference as a result, quit dentalcnc and restart the application.
To avoid connecting errors, we highly recommend that you use the USB or Ethernet cable which was provided with the device. Original spare parts are available from customer service.